SAS Breschard
le spécialiste de la manutention continue vrac.

Questions / Réponses sur la production de SAS Breschard
Quel matériel utiliser pour de la manutention continue ?
La manutention continue fait référence à des systèmes de transport ou de manipulation de charges de manière ininterrompue sur une longue période. Ce type de manutention est généralement utilisé dans des environnements industriels, logistiques ou de production où les matériaux doivent être déplacés sans interruption, souvent dans un flux continu.
Le matériel utilisé pour la manutention continue varie en fonction du type de matériau à transporter (en vrac, palettes, caisses, etc.) et de l’environnement de travail (entrepôt, usine, etc.). Voici les principaux types de matériels utilisés pour la manutention continue :
1. Transporteurs à bande (Convoyeurs à bande)
- Description : Les transporteurs à bande sont utilisés pour déplacer des matériaux de manière continue sur une bande enroulée autour de rouleaux. La bande transporteuse peut être en caoutchouc, PVC, ou encore en métal, selon le type de matériaux manipulés.
- Applications : Transport de palettes, cartons, matériaux en vrac, ou pièces manufacturées dans des lignes de production, entrepôts, centres de distribution.
- Avantages :
- Idéal pour des distances longues et des déplacements continus.
- Adapté à tous types de matériaux, y compris les petits objets, les pièces légères ou les charges en vrac.
- Peut être utilisé pour transporter à hauteur variable (pentes ou descentes).
2. Convoyeurs à rouleaux
- Description : Un convoyeur à rouleaux utilise une série de rouleaux montés sur un châssis pour déplacer des charges. Les rouleaux peuvent être motorisés ou non. Ce type de convoyeur est particulièrement adapté pour des charges palettisées ou de grandes dimensions.
- Applications : Déplacement de caisses, palettes, conteneurs, ou charges lourdes dans des entrepôts, des zones de production ou des centres de tri.
- Avantages :
- Convient aux charges rigides et palettisées.
- Peut être intégré avec des systèmes de tri ou des systèmes automatiques.
- Permet une manipulation continue sans interruption, surtout en combinaison avec un système motorisé.
3. Transporteurs à chaîne
- Description : Les transporteurs à chaîne utilisent une chaîne comme élément de traction pour déplacer des charges. Cette solution est idéale pour les matériaux lourds ou volumineux.
- Applications : Transport de matériaux lourds comme des pièces métalliques, caisses, palettes, ou des pièces d’assemblage dans des ateliers, usines ou chaînes de production.
- Avantages :
- Très robuste et adapté pour les charges lourdes ou encombrantes.
- Peuvent être utilisés dans des environnements difficiles (températures élevées, poussières, etc.).
- Manipulation continue, sans interruption.
4. Systèmes de palettes roulantes ou monorail aérien
- Description : Un monorail aérien est un système de rails suspendus où des palettes ou des charges sont déplacées par un chariot suspendu. Ces systèmes sont souvent utilisés pour le transport de matériaux dans des usines ou des ateliers où l'espace au sol est limité.
- Applications : Idéal pour des matériaux qui nécessitent un transport vertical ou qui doivent être déplacés dans des espaces restreints.
- Avantages :
- Optimisation de l'espace en utilisant la hauteur.
- Manipulation continue de charges légères à lourdes sur des distances courtes à moyennes.
- Convient aux environnements où des modifications de hauteur sont nécessaires.
5. Élévateurs à godets
- Description : Les élévateurs à godets sont des dispositifs utilisés pour transporter des matériaux en vrac ou en morceaux (sable, gravier, céréales, etc.) dans des conteneurs en forme de godets fixés à une chaîne ou à une bande.
- Applications : Très utilisés dans l'industrie alimentaire, le secteur de la construction, ou le traitement des déchets pour déplacer des matériaux en vrac de manière continue, généralement sur de grandes hauteurs.
- Avantages :
- Transport vertical de matériaux en vrac, avec une haute capacité de charge.
- Fonctionne de manière continue et permet de déplacer des quantités massives de matériaux.
6. Systèmes de transporteurs à vis (ou vis sans fin)
- Description : Un transporteur à vis utilise une vis rotative pour déplacer des matériaux en vrac ou semi-solides le long d'un tube ou d'un canal. Il est particulièrement adapté pour les matériaux comme les poudres, les grains, ou les granulés.
- Applications : Transfert de matériaux poudrés, granulés, ou en vrac dans les secteurs agricoles, chimiques, alimentaires et industriels.
- Avantages :
- Utilisé pour des matériaux en vrac ou des produits difficiles à transporter sur des distances courtes à moyennes.
- Manipulation continue et efficace pour des matériaux granulés ou en poudre.
7. Convoyeurs à bande modulaire (ou à maillons)
- Description : Un convoyeur à bande modulaire est un type de transporteur qui utilise des modules en plastique ou en acier inoxydable interconnectés pour former une surface continue. Ce système est particulièrement utilisé pour le transport de produits dans des industries alimentaires, pharmaceutiques, ou des environnements où une hygiène stricte est nécessaire.
- Applications : Utilisé dans les lignes de production pour transporter des produits finis, des composants dans des environnements propres, ou encore des emballages.
- Avantages :
- Flexible : peut être configuré pour des distances variables, des angles différents ou des configurations complexes.
- Très facile à nettoyer et à entretenir, particulièrement dans les secteurs où l'hygiène est essentielle.
- Manipulation continue, sans interruption.
8. Tapis roulants pour manutention
- Description : Les tapis roulants sont similaires aux transporteurs à bande, mais souvent plus petits et plus flexibles. Ils sont utilisés pour déplacer des matériaux ou des produits d'un point à un autre à l'intérieur d'un entrepôt ou d'une zone de production.
- Applications : Idéal pour des produits légers comme des cartons, des colis, ou des paquets dans des entrepôts, centres de distribution, ou installations logistiques.
- Avantages :
- Solution simple et économique pour un transport horizontal de produits.
- Utilisé pour des petites charges légères, mais peut être adapté pour des charges lourdes selon les matériaux.
9. Convoyeur à bande modulaire
- Description : Ce type de convoyeur utilise des modules de plastique ou métal pour former une bande de transport. Ces modules peuvent être facilement remplacés ou ajustés selon les besoins.
- Applications : Convient pour des lignes de production, des emballages, des produits alimentaires, etc.
- Avantages :
- Facilité de maintenance.
- Idéal pour des charges légères à moyennes.
- Adapté aux environnements qui nécessitent une hygiène stricte (comme l'agroalimentaire).
Conclusion
Les équipements de manutention continue sont cruciaux pour améliorer l'efficacité dans des environnements industriels ou logistiques où des matériaux doivent être déplacés sans interruption. Le choix du matériel dépendra de plusieurs facteurs, tels que la nature des matériaux (en vrac, palettes, objets divers), la distance à parcourir, la charge à soulever, et l'environnement (espaces confinés, conditions de sécurité, etc.).
Principaux critères de sélection :
- Type de matériau (vrac, objets ou palettes).
- Poids et dimensions des charges.
- Espace disponible (si l'espace est limité, un monorail ou un convoyeur aérien peut être nécessaire).
- Capacité de production continue ou de transport sans interruption.
Quels sont les différents transporteurs à bande ?
Les transporteurs à bande sont des systèmes de convoyage qui utilisent une bande continue pour déplacer des matériaux d’un point à un autre. Ces systèmes sont largement utilisés dans de nombreuses industries, y compris l'industrie minière, la logistique, l’agroalimentaire, et la production industrielle. Il existe plusieurs types de transporteurs à bande, chacun ayant des caractéristiques spécifiques en fonction de l'application et de l'environnement d'utilisation. Voici les principaux types :
1. Transporteur à bande à rouleaux
- Ce type de transporteur utilise une série de rouleaux pour faire passer la bande et transporter les objets.
- Les rouleaux peuvent être entraînés ou simplement destinés à guider la bande.
- Ils sont utilisés dans des applications où la charge à transporter est relativement légère à moyenne.
2. Transporteur à bande modulaire
- La bande est composée de segments individuels, souvent en plastique ou en métal, reliés entre eux.
- Ce type est particulièrement utile pour les environnements nécessitant une flexibilité accrue, car la bande peut être facilement modifiée ou réparée.
- Il est couramment utilisé dans l'industrie alimentaire et les lignes de production.
3. Transporteur à bande à faible pente
- Ce modèle est conçu pour transporter des matériaux sur une pente douce, souvent utilisé pour des tâches telles que le transport de sable, de gravier ou d'autres matériaux en vrac.
- Il peut être incliné à un angle modéré pour faciliter le déchargement de matériaux.
4. Transporteur à bande incliné
- Ce type de transporteur est conçu pour transporter des matériaux sur des pentes plus importantes.
- Il peut être équipé de bandes avec des bords repliés (bandes bordées) ou de bandes à trous pour éviter que les matériaux ne tombent.
5. Transporteur à bande à haute résistance
- Ces transporteurs sont utilisés pour les applications les plus exigeantes, comme le transport de matériaux lourds, abrasifs ou chauds.
- La bande est souvent renforcée avec des câbles métalliques ou des fibres spéciales pour supporter des charges lourdes.
6. Transporteur à bande à vis sans fin (ou visée)
- Bien qu’il ne s’agisse pas exactement d’un transporteur à bande au sens traditionnel, il fonctionne sur un principe similaire en utilisant une vis sans fin pour transporter des matériaux dans un tube ou un canal.
7. Transporteur à bande à poche (ou à godets)
- Ce système utilise des poches ou des godets fixés à intervalles réguliers sur la bande pour transporter des matériaux en vrac vers le haut ou sur des surfaces inclinées.
- C’est une solution idéale pour transporter des matériaux tels que des grains, des poudres ou des granulats.
8. Transporteur à bande en caoutchouc
- Ces transporteurs sont utilisés dans des environnements où une bande en caoutchouc est nécessaire pour une meilleure adhérence ou pour transporter des matériaux avec des surfaces glissantes.
- Ils sont courants dans les industries de traitement des matériaux, de recyclage, et de l’extraction minière.
9. Transporteur à bande pour environnement alimentaire
- Ce type de transporteur est conçu pour répondre aux normes sanitaires strictes de l’industrie alimentaire. Il utilise des matériaux résistants aux agents de nettoyage et aux conditions de traitement alimentaire.
- Les bandes sont souvent fabriquées en plastique, en inox ou en autres matériaux approuvés pour un contact alimentaire.
10. Transporteur à bande tubulaire
- Ce système est utilisé pour transporter des matériaux en vrac, tout en les protégeant de l'extérieur.
- La bande est enroulée dans un tube ou un conduit fermé, ce qui permet de réduire la poussière et les risques de contamination.
11. Transporteur à bande à bande étroite
- Ce type de transporteur utilise une bande étroite pour transporter de petites charges ou des articles délicats.
- Il est souvent utilisé pour des lignes de production ou des applications de tri automatisé.
12. Transporteur à bande en pente variable
- Ce modèle permet de modifier l'angle de la pente selon les besoins, offrant une flexibilité pour s'adapter à différents types de matériaux et d'installations.
En fonction des besoins spécifiques de l’application (type de produit, environnement, capacité de charge, distance de transport, etc.), un transporteur à bande peut être conçu et adapté pour maximiser l'efficacité du transport.
Pourquoi utiliser un chariot verseur sur un transporteur à bande ?
L'utilisation d'un chariot verseur sur un transporteur à bande est une solution courante dans de nombreux systèmes de manutention pour plusieurs raisons pratiques et techniques. Le rôle principal du chariot verseur est de réaliser un déversement contrôlé et précis des matériaux transportés par la bande transporteuse à un endroit spécifique. Voici les principales raisons pour lesquelles un chariot verseur est utilisé avec un transporteur à bande :
1. Contrôle précis du déversement
Le chariot verseur permet de contrôler avec précision le moment et l'emplacement du déversement des matériaux transportés. Il est souvent conçu pour permettre un mouvement de rotation ou d'inclinaison qui dirige le flux de matériaux de manière régulière et uniforme, ce qui est crucial dans les processus industriels où une répartition précise des matériaux est nécessaire.
2. Eviter les pertes ou les gaspillages
Dans les systèmes de transport de matériaux en vrac, un chariot verseur permet de réduire le risque de pertes de matériaux pendant le processus de déversement. Sans un déversement contrôlé, les matériaux pourraient tomber de manière désordonnée, ce qui peut entraîner des pertes ou des débordements, particulièrement dans des applications où l'efficacité et l'économie sont essentielles.
3. Éviter l'accumulation ou les obstructions
En utilisant un chariot verseur, on peut éviter les accumulations locales ou les obstructions des matériaux à un point donné du convoyeur. Par exemple, lorsque des matériaux en vrac (comme des granulés, des poudres, des cailloux ou des déchets) sont transportés, un déversement incontrôlé pourrait créer une zone d'encombrement qui pourrait bloquer ou gêner l'écoulement de matériaux sur la bande.
4. Amélioration de la productivité
Le chariot verseur permet de déverser de manière plus rapide et plus contrôlée sur des lignes de production ou de stockage. Il permet d'optimiser les délais de traitement et de réduire les risques d'interruptions ou de retards dus à des déversements maladroits ou imprévus. Cela contribue à améliorer la productivité globale du système de transport.
5. Sécurité accrue
Un chariot verseur permet d’effectuer un déversement à une hauteur et à un endroit spécifiques, minimisant ainsi les risques pour les opérateurs et réduisant le besoin d’interventions manuelles dangereuses près de la bande transporteuse. Les matériaux peuvent être dirigés de manière sécurisée dans un conteneur ou un espace désigné, réduisant les risques d’accidents ou de blessures.
6. Adaptabilité aux différents matériaux
Les chariots verseurs sont souvent conçus pour être ajustables en fonction du type de matériaux transportés. Que ce soit des matériaux lourds, légers, solides ou en poudre, le chariot verseur peut être adapté pour garantir un déversement sans endommager les matériaux ni créer de nuisance (poussières ou éclaboussures par exemple). Cette flexibilité est particulièrement importante dans des secteurs comme l’industrie chimique, alimentaire, ou dans les systèmes de recyclage.
7. Facilité d'intégration dans des systèmes automatisés
Les chariots verseurs motorisés ou automatisés peuvent être intégrés dans des systèmes de production automatisés ou de gestion des stocks, permettant un déversement précis sans intervention humaine. Cela améliore l'efficacité du processus, tout en assurant une gestion homogène et constante des flux de matériaux.
8. Réduction de la maintenance
Un déversement contrôlé et uniformément réparti permet de réduire l’usure prématurée des autres équipements du système de transport (comme la bande transporteuse elle-même, les moteurs ou les convoyeurs en aval), ce qui peut conduire à une réduction des coûts de maintenance et à une longévité accrue de l'ensemble du système.
9. Optimisation de l'espace de stockage ou de production
Le chariot verseur permet d'envoyer les matériaux dans des zones spécifiques pour être stockés, manipulés ou traités selon les besoins de la production. Cela optimise l'utilisation de l'espace en dirigeant les matériaux vers des zones bien définies, qu’il s’agisse de bacs, de silos ou d’autres équipements de stockage.
10. Réduction du bruit et de la poussière
Un chariot verseur peut également être conçu pour réduire les nuisances sonores et la production de poussière lors du déversement, ce qui est particulièrement important dans des environnements de travail où ces facteurs sont un problème. Par exemple, un chariot verseur bien conçu peut diriger les matériaux de manière douce dans un réceptacle, limitant ainsi les éclaboussures et les projections de poussières.
Conclusion
Le chariot verseur utilisé sur un transporteur à bande est donc un accessoire indispensable dans de nombreux systèmes industriels où un déversement précis et contrôlé des matériaux en vrac est nécessaire. Il permet de garantir un écoulement efficace, de réduire les pertes et les gaspillages, d'améliorer la sécurité, et de faciliter l'automatisation des processus de production ou de manutention. Sa polyvalence, combinée à la possibilité de l’adapter à divers types de matériaux et d’applications, en fait un équipement clé pour optimiser la gestion des flux de matériaux dans de nombreuses industries.
Qu'est-ce qu'un transporteur bande à bord ?
Un transporteur à bande à bord (également appelé convoyeur à bande avec bords ou convoyeur à bande avec bords repliés) est un type de convoyeur à bande équipé de bords relevés ou de bords latéraux sur les côtés de la bande. Ces bords sont généralement fabriqués à partir du même matériau que la bande ou d'un matériau complémentaire, et leur rôle principal est de contenir et de guider les matériaux qui sont transportés sur la bande.
Fonctionnement et caractéristiques du transporteur à bande à bord :
-
Bords latéraux (ou bordures) :
- Les bords repliés ou les bords latéraux sont généralement positionnés sur toute la longueur des côtés de la bande transporteuse, formant une sorte de rempart ou canal qui empêche les matériaux de tomber ou de déborder du convoyeur pendant leur transport.
- Ces bords peuvent être faits en caoutchouc, en acier, en plastique ou d'autres matériaux résistants, selon les exigences spécifiques du processus ou du type de matériau transporté.
-
Types de bords :
- Bords fixes : Ce sont des bords solidement fixés sur les côtés de la bande, sans possibilité de mouvement. Ils sont généralement soudés ou fixés mécaniquement à la bande.
- Bords repliés : Il s'agit de bords fabriqués directement à partir de la bande, souvent en repliant les bords de la bande de manière à les relever. Ce type de bord est plus économique et est souvent utilisé pour des applications simples.
- Bords modulaires : Dans certains cas, les bords peuvent être modulaires, ce qui permet de les remplacer ou d'ajuster leur hauteur en fonction des besoins.
-
Hauteur des bords :
- La hauteur des bords peut varier en fonction du type de matériau transporté et des exigences spécifiques de l'application. Par exemple, pour les matériaux légers, les bords peuvent être relativement bas, tandis que pour des matériaux plus lourds ou en vrac, les bords peuvent être plus hauts pour éviter tout débordement.
-
Matériaux des bords :
- Les bords peuvent être fabriqués en caoutchouc (souvent pour des applications où l'élasticité est requise), en plastique (plus léger et souvent utilisé pour des applications de faible poids), ou en métal (comme l’acier inoxydable ou le galvanisé) pour des applications plus lourdes et dans des environnements industriels plus exigeants.
Avantages d'un transporteur à bande à bord :
-
Prévention des déversements :
- Les bords latéraux empêchent les matériaux en vrac ou liquides de se renverser, particulièrement lorsqu'ils sont transportés sur des surfaces inclinées ou lorsqu'ils présentent des risques de débordement.
-
Contrôle amélioré du flux :
- Le fait d'avoir des bords aide à canaliser le matériau de manière plus précise sur la bande, évitant ainsi qu'il ne se déplace latéralement ou qu'il ne s'échappe du système de transport. Cela est particulièrement utile lorsque les matériaux sont de formes irrégulières ou qu'ils présentent des caractéristiques comme des poudres fines ou des granulés qui peuvent facilement déborder.
-
Réduction des pertes de matériau :
- Les bords permettent de réduire les pertes de matériaux pendant le transport. Cela est particulièrement important dans les applications où le matériau est coûteux, difficile à récupérer ou doit être traité de manière spécifique (par exemple, dans les industries alimentaires ou pharmaceutiques).
-
Amélioration de la sécurité :
- En empêchant le matériau de tomber hors du convoyeur, les bords latéraux contribuent à maintenir la sécurité sur le site de travail. Cela peut également éviter les obstructions dans l’environnement de travail ou dans les autres équipements en aval.
-
Adaptabilité aux matériaux en vrac :
- Les bords sont particulièrement utiles pour le transport de matériaux en vrac, tels que des granulats, des poudres, des produits agricoles ou des déchets solides, où le risque de déversement est élevé sans une barrière.
-
Application flexible :
- Le transporteur à bande à bord peut être utilisé dans des applications diverses, des plus simples aux plus complexes, en fonction de l'industrie et du type de produit. Il peut être utilisé pour des produits légers ou des produits lourds, et peut être configuré pour s’adapter à une large gamme de débits et de tailles de matériaux.
Applications typiques du transporteur à bande à bord :
- Industrie alimentaire :
- Pour transporter des produits alimentaires (p. ex., fruits, légumes, céréales, bonbons) où les risques de contamination ou de pertes sont importants.
- Industrie minière et des matériaux de construction :
- Pour transporter des sables, des graviers, des minerais ou d'autres matériaux en vrac, en particulier dans les conditions difficiles où le contrôle des matériaux est crucial.
- Industrie chimique :
- Pour des matériaux chimiques sous forme de poudre ou de granulés, afin de prévenir tout déversement ou contamination.
- Recyclage :
- Dans les centres de recyclage pour transporter des matériaux en vrac comme du plastique ou des métaux tout en évitant les pertes et en améliorant l'efficacité du système.
- Logistique et manutention :
- Pour la gestion du transport des produits et matériaux dans des entrepôts ou des zones de production où le contrôle du flux est essentiel.
Conclusion
Le transporteur à bande à bord est donc une solution efficace pour le transport de matériaux en vrac, notamment dans des situations où le contrôle du flux et la prévention des pertes sont essentiels. Grâce à la présence de bords latéraux, il permet de canaliser les matériaux, d'éviter les déversements et de garantir une manutention plus sécurisée et plus optimisée des matériaux transportés.
Qu'est-ce qu'un convoyeur à vis ?
Un convoyeur à vis (ou vis sans fin) est un système de transport utilisé pour déplacer des matériaux en vrac, granuleux ou en poudre à l’intérieur d’un tube ou d’une goulotte, grâce à une vis rotative. Ce système est souvent employé dans des industries comme l'agriculture, la chimie, l’alimentation, le recyclage, ou dans les centrales de traitement de matériaux.
Fonctionnement du convoyeur à vis
Le principe de fonctionnement repose sur une vis hélicoïdale (ou vis sans fin) qui tourne à l’intérieur d’un tube ou d’un canal. Lorsque la vis tourne, elle pousse le matériau à travers le tube, d'un point d'entrée vers un point de sortie.
-
Vis rotative : La vis, généralement fabriquée en acier ou en matériaux résistants à l'usure, est montée sur un arbre rotatif qui tourne dans un tube ou un canal. Le mouvement de rotation fait avancer les matériaux qui se trouvent dans la vis.
-
Conteneur fermé : Le convoyeur à vis est souvent utilisé dans un tube fermé pour éviter la dispersion de matériaux (comme la poussière) ou pour protéger le produit du contact avec l'extérieur.
-
Angle d'inclinaison : Le convoyeur à vis peut être incliné à divers angles, selon le type de matériau à transporter et la configuration de l’installation. Cependant, à des angles trop importants, l’efficacité de transport peut diminuer.
Types de convoyeurs à vis
Il existe plusieurs types de convoyeurs à vis, en fonction des besoins spécifiques de l’application :
-
Convoyeur à vis horizontale : Le transport des matériaux se fait sur un axe horizontal. Ce type est utilisé pour des distances relativement courtes.
-
Convoyeur à vis incliné : La vis fonctionne à un angle incliné pour transporter les matériaux vers le haut ou sur une pente. Plus l'inclinaison est grande, plus il peut être difficile de transporter des matériaux lourds ou visqueux, car la charge risque de retomber.
-
Convoyeur à vis vertical : Ce type permet de transporter des matériaux sur de grandes hauteurs. Il est particulièrement utilisé pour soulever des produits à des altitudes plus élevées tout en conservant un espace réduit.
-
Convoyeur à vis flexible (ou vis mobile) : Il s'agit d'une version modulaire du convoyeur à vis, souvent utilisée dans le transport de produits en vrac dans des espaces de stockage ou des zones de manutention temporaire. Ce système est flexible et peut être ajusté en longueur et orientation.
Avantages des convoyeurs à vis
-
Transport de matériaux en vrac : Ils sont particulièrement adaptés pour les matériaux en vrac, tels que le sable, les cendres, les grains, les semences, les poudres, les pellets, etc.
-
Compact et flexible : Ils sont relativement compacts et peuvent être installés dans des espaces réduits. Leur design permet une installation horizontale, inclinée ou verticale en fonction des besoins.
-
Capacité de transport contrôlable : La vitesse de rotation de la vis permet de réguler le débit de transport du matériau, ce qui permet d’adapter la capacité de transport selon les besoins spécifiques.
-
Moins de risque de contamination : Étant souvent utilisés dans des environnements fermés, les convoyeurs à vis limitent la dispersion des matériaux, ce qui réduit les risques de contamination (particulièrement dans les industries alimentaires et pharmaceutiques).
Inconvénients
-
Limitation de la distance : Les convoyeurs à vis ne sont généralement pas efficaces pour de très longues distances, car la capacité de transport diminue avec la longueur du tube et l'angle de la vis.
-
Usure de la vis : Les matériaux abrasifs peuvent accélérer l'usure de la vis. Une maintenance régulière est donc nécessaire pour éviter la détérioration du système.
-
Capacité limitée pour des matériaux très denses ou collants : Les matériaux lourds ou ayant des caractéristiques particulières (par exemple, visqueux ou humides) peuvent être difficiles à transporter avec une vis sans fin.
Applications courantes des convoyeurs à vis
- Agriculture : Transport de grains, semences, engrais, etc.
- Industrie alimentaire : Transport de farine, sucre, sel, cacao en poudre, etc.
- Industrie chimique : Convoyage de poudres, granulés ou produits chimiques en vrac.
- Traitement des eaux usées : Convoyage de boues ou de solides dans le traitement des eaux.
- Recyclage : Transport de déchets recyclables tels que le plastique, le verre, le métal, etc.
En résumé, un convoyeur à vis est un outil polyvalent et efficace pour transporter des matériaux en vrac sur des distances relativement courtes ou verticalement, dans des environnements où d'autres systèmes de convoyage (comme les convoyeurs à bande) ne seraient pas aussi efficaces.
Qu'est-ce qu'une trémie à casque ?
Une trémie à casque est un type particulier de trémie conçu pour l’alimentation ou le déchargement de matériaux en vrac dans des systèmes de convoyage ou de stockage. Ce type de trémie se caractérise par un dispositif de contrôle de l’écoulement des matériaux, souvent sous la forme d’un casque ou d’une cloche situé au bas de la trémie. Le casque joue un rôle crucial dans la gestion du flux de matière, en particulier pour garantir un écoulement régulier et contrôlé.
Fonctionnement d'une trémie à casque
Le terme "casque" dans trémie à casque fait référence à une structure en forme de cône ou de cloche placée à l'ouverture inférieure de la trémie. Cette structure aide à orienter le flux de matériaux et peut être équipée de dispositifs qui permettent de réguler ou de bloquer l’écoulement pour éviter les fuites incontrôlées de matières.
Voici les principaux éléments de fonctionnement d'une trémie à casque :
-
Contrôle du flux de matière : Le casque permet un contrôle précis de l'écoulement des matériaux en vrac, en particulier pour éviter qu'ils ne s’écoulent trop rapidement ou de manière irrégulière, ce qui pourrait entraîner des pertes de matériau ou endommager les équipements en aval.
-
Répartition uniforme : Le casque aide à répartir uniformément le flux de matière vers les convoyeurs ou autres équipements de traitement. Cela est particulièrement utile dans des systèmes où une distribution uniforme du produit est nécessaire.
-
Évitement de l'agglutination ou du blocage : Dans certains cas, le casque aide à empêcher l’agglutination des matériaux ou des blocages dans la trémie, en particulier lorsque les matériaux sont susceptibles de se coller ensemble (par exemple, les poudres fines ou les granulés humides).
-
Adaptabilité : Les trémies à casque peuvent être conçues pour différents types de matériaux, tels que des poudres, des granulés, ou des produits en vrac. Le design du casque peut être ajusté en fonction de la taille et de la consistance du matériau manipulé.
-
Vitesse d'écoulement contrôlée : Dans certaines applications, la trémie à casque peut être équipée de mécanismes pour contrôler la vitesse d'écoulement du matériau, comme des vannes à guillotine ou des clapets, pour ralentir ou arrêter l'écoulement quand cela est nécessaire.
Applications des trémies à casque
Les trémies à casque sont couramment utilisées dans des industries où il est important de stocker, doser et/ou transférer des matériaux en vrac de manière contrôlée, comme :
- Industrie alimentaire : Pour le stockage et le transfert de farine, sucre, grains, ou autres ingrédients en vrac.
- Industrie chimique et pharmaceutique : Pour la gestion de poudres, granulés ou produits chimiques.
- Industrie des matériaux de construction : Pour l'alimentation de convoyeurs ou autres équipements avec des matériaux en vrac tels que le ciment, le sable, ou les granulats.
- Traitement des déchets : Pour stocker et gérer les déchets solides ou le recyclage des matériaux.
Conclusion
La trémie à casque est donc une solution efficace pour gérer l’écoulement de matériaux en vrac, en assurant une distribution uniforme, un contrôle précis du flux et en minimisant les risques de blocages ou de pertes. Elle est souvent utilisée dans des secteurs industriels nécessitant un contrôle strict des matériaux transportés ou stockés.
Pourquoi utiliser un élévateur à godets plutôt qu'un transporteur à bande ?
L’utilisation d'un élévateur à godets plutôt que d’un transporteur à bande dépend des spécificités de l'application, des caractéristiques du produit à transporter et des exigences techniques du système de transport. Les élévateurs à godets et les transporteurs à bande sont tous deux des systèmes de convoyage, mais ils présentent des différences notables qui les rendent adaptés à des situations spécifiques. Voici quelques raisons pour lesquelles vous pourriez opter pour un élévateur à godets plutôt qu'un transporteur à bande :
1. Transport de matériaux sur de grandes hauteurs
- Élévateur à godets : Les élévateurs à godets sont spécialement conçus pour soulever des matériaux en vrac vers des hauteurs importantes. Ils peuvent transporter des matériaux verticalement sur des distances relativement longues sans perte de capacité ou d'efficacité. C'est un choix idéal si vous devez déplacer des matériaux sur plusieurs niveaux ou sur des installations de grande hauteur (ex : de l’entrepôt à la zone de stockage supérieure).
- Transporteur à bande : Bien qu'il existe des transporteurs à bande inclinés ou verticaux, ils ne sont généralement pas aussi efficaces pour des élévations verticales importantes, surtout pour des matériaux lourds ou volumineux.
2. Gestion de matériaux en vrac lourds ou abrasifs
- Élévateur à godets : Les godets permettent de manipuler des matériaux lourds, abrasifs, ou en grandes quantités (comme le charbon, le sable, le ciment, ou les granulats) sans que le produit ne soit comprimé ou endommagé. Les matériaux sont "poussés" dans les godets et maintenus en place pendant leur transport.
- Transporteur à bande : Bien que les transporteurs à bande puissent également transporter des matériaux lourds, leur capacité est limitée par la friction et la tension exercées sur la bande. Pour les matériaux abrasifs, il peut y avoir une usure plus rapide de la bande et des composants, ce qui nécessite des matériaux renforcés ou une maintenance plus fréquente.
3. Capacité à transporter des matériaux à forte granulométrie ou volumineux
- Élévateur à godets : Il est particulièrement adapté pour le transport de matériaux en vrac à forte granulométrie (graviers, éclats de roche, etc.), ou pour des produits qui risqueraient de tomber ou de se répandre sur une bande transporteuse. Les godets sont conçus pour contenir et déplacer ces matériaux sans que ceux-ci ne se dispersent.
- Transporteur à bande : Les matériaux volumineux ou irréguliers peuvent poser des problèmes sur un convoyeur à bande, car ils risquent de tomber, de rouler ou de s’échapper de la bande, surtout si la bande n’est pas équipée de bords repliés ou de ridelles.
4. Réduction de l'encombrement au sol
- Élévateur à godets : Étant conçu pour un transport vertical, un élévateur à godets occupe généralement moins d’espace au sol. Si l'espace est limité ou que vous avez besoin de maximiser l'utilisation de la surface horizontale, un élévateur à godets est un choix plus approprié.
- Transporteur à bande : Bien qu’il existe des versions inclinées et verticales, les transporteurs à bande ont tendance à être plus longs et plus larges, surtout lorsqu’ils transportent des matériaux sur de grandes distances.
5. Moins de risques de contamination ou de dispersion
- Élévateur à godets : En raison de sa conception fermée, un élévateur à godets est mieux adapté pour contenir des matériaux en vrac, limitant la dispersion de poussières ou de matériaux volatils. Cela est particulièrement utile dans des secteurs comme l'agroalimentaire, la chimie ou le recyclage, où la propreté et la gestion de la poussière sont importantes.
- Transporteur à bande : Même avec des bords repliés ou une bande fermée, un transporteur à bande présente plus de risques de dispersion de matériaux, surtout si ceux-ci sont poussiéreux ou légers.
6. Moins de besoin en maintenance (pour certains matériaux)
- Élévateur à godets : Il est souvent plus facile à entretenir dans les applications de transport de matériaux lourds ou abrasifs. Les godets et les chaînes ou courroies qui les entraînent sont relativement robustes et peuvent supporter de telles conditions sans une usure rapide.
- Transporteur à bande : Les bandes peuvent souffrir de l’usure prématurée, en particulier pour des matériaux abrasifs, ce qui nécessite un remplacement ou une réparation plus fréquente.
7. Transport sur de longues distances avec un faible encombrement
- Élévateur à godets : Bien que limité en termes de vitesse par rapport à certains transporteurs à bande, il peut transporter des matériaux sur de longues distances verticalement tout en réduisant l’espace au sol requis. Cela le rend adapté aux environnements où l'espace horizontal est limité mais où un transport vertical est nécessaire.
- Transporteur à bande : Pour des distances horizontales longues, le transporteur à bande est plus efficace, mais l’encombrement au sol peut devenir un problème.
8. Convient aux matériaux collants ou visqueux
- Élévateur à godets : Les godets sont souvent conçus pour manipuler des matériaux collants ou visqueux (comme des pâtes ou des produits semi-solides), qui peuvent être difficiles à transporter avec des bandes. La conception du godet permet de contenir et déplacer ces matériaux sans les écraser ou les faire adhérer à une bande.
- Transporteur à bande : Pour des matériaux collants ou visqueux, les bandes peuvent devenir moins efficaces, car ces matériaux peuvent se coller à la surface de la bande et provoquer des blocages ou des déformations.
En résumé :
Le choix entre un élévateur à godets et un transporteur à bande dépend principalement des caractéristiques des matériaux à transporter, de l’espace disponible, de la hauteur de levée nécessaire et des exigences spécifiques en termes de capacité et d’encombrement. Un élévateur à godets est idéal pour :
- Le transport de matériaux en vrac lourds, abrasifs, ou de grande granulométrie.
- Les déplacements verticaux ou sur de grandes hauteurs.
- Les matériaux volatils ou poussiéreux.
- Les applications où l’espace au sol est limité.
En revanche, un transporteur à bande est mieux adapté pour :
- Le transport horizontal ou légèrement incliné de matériaux en vrac légers.
- Les applications où une longue distance horizontale est requise.
- Les matériaux non abrasifs et non collants.
Quelle est la différence entre un retourneur basculeur et un skip ?
Pourquoi utiliser un skip élévateur basculeur ?
Quel est la différence entre l'oxycoupage et le découpage avec un plasma haute définition ?
L'oxycoupage et le découpage plasma haute définition sont deux procédés utilisés pour la découpe de métaux, mais ils diffèrent à la fois par leur principe de fonctionnement, leurs applications et la qualité des découpes qu'ils produisent. Voici une comparaison détaillée des deux méthodes :
1. Principe de fonctionnement :
-
- L'oxycoupage est un procédé de découpe thermique qui repose sur une réaction chimique entre l'oxygène pur et le métal. La coupe est réalisée en chauffant le métal à son point de fusion avec une flamme oxyacétylénique (mélange d’oxygène et de gaz carburant comme l’acétylène) ou simplement avec de l'oxygène pur pour des métaux ferreux comme l'acier.
- Lorsque la température atteint environ 1 200-1 500 °C, l'oxygène réagit avec le fer ou l’acier pour former de l’oxyde de fer (rouille), ce qui crée une perte de métal et permet de découper la pièce.
- Le gaz oxygéné est utilisé pour souffler le métal fondu et l'oxyde, créant ainsi une coupe nette.
-
Découpage plasma haute définition :
- Le découpage plasma utilise un jet de gaz ionisé (plasma) à très haute température (jusqu'à 30 000 °C). Ce gaz est pressurisé et expulsé à grande vitesse à travers une buse étroite. Lorsque le gaz plasma entre en contact avec le métal, il chauffe celui-ci à une température suffisamment élevée pour le fondre et le souffler loin de la coupe.
- Le procédé peut être utilisé avec une grande variété de métaux, y compris les métaux non ferreux (aluminium, inox, cuivre), ce que l'oxycoupage ne permet pas.
2. Qualité de la coupe :
-
- Le traitement de surface est plus grossier comparé au découpage plasma. L'oxycoupage laisse souvent des bords rugueux, avec des résidus d'oxyde et des zones plus larges de zone affectée thermiquement.
- L'angle de coupe n'est pas aussi précis, et le bords de coupe peuvent être irréguliers (notamment pour des matériaux épais).
- Ce procédé est plus adapté pour des applications où la précision n'est pas aussi critique, et généralement pour des matériaux épais comme l'acier doux.
-
Découpage plasma haute définition :
- Le découpage plasma haute définition offre une très haute précision et une meilleure qualité de coupe que l'oxycoupage. Grâce à une buse plus fine et un plasma plus concentré, les bords de coupe sont beaucoup plus nets, avec moins de zones affectées thermiquement.
- Le nettoyage des bords est moins nécessaire, car il y a moins de résidus d'oxyde.
- Les angles sont plus précis et les dimensions de la coupe sont très fidèles à la commande numérique, permettant des découpes complexes et de petites tailles avec une grande précision.
3. Applications :
-
- L'oxycoupage est principalement utilisé pour des matériaux ferreux comme l’acier au carbone et certains alliages d'acier. Il est particulièrement efficace pour les matériaux épais, souvent de 6 mm à 300 mm, et c'est un procédé assez économique pour ces applications.
- Il est souvent utilisé dans des secteurs comme la construction métallique, la démolition, et la réparation de structures métalliques.
- L'oxycoupage est plus limité avec des matériaux non ferreux comme l'aluminium ou l'acier inoxydable, car ces métaux ne réagissent pas aussi facilement avec l'oxygène.
-
Découpage plasma haute définition :
- Le découpage plasma haute définition est plus polyvalent, capable de découper des matériaux ferreux (acier, fonte, etc.), mais aussi des matériaux non ferreux (aluminium, inox, cuivre, etc.), ce qui lui confère un champ d’application plus large.
- Ce procédé est largement utilisé dans les industries de l'automobile, l'aéronautique, la construction navale, l'industrie métallurgique, et pour les applications nécessitant des découpes de précision.
- Le découpage plasma haute définition est idéal pour des pièces de petite à moyenne épaisseur (souvent jusqu'à 100 mm), mais avec une très haute précision.
4. Vitesse de coupe :
-
- Le procédé est relativement rapide pour les matériaux épais, mais la vitesse dépend de l'épaisseur du métal à couper. Les coupes plus lentes peuvent être nécessaires pour des matériaux plus fins ou plus durs.
- En général, il est plus rapide que le découpage plasma pour des matériaux très épais (plus de 30 mm).
-
Découpage plasma haute définition :
- Le découpage plasma haute définition est généralement plus rapide que l'oxycoupage pour les matériaux de moyenne épaisseur (moins de 30 mm), tout en offrant une meilleure qualité de coupe.
- Cependant, il est moins rapide pour les matériaux très épais (plus de 30 mm), où l'oxycoupage peut être plus efficace pour des coupes rapides.
5. Coûts :
- Oxycoupage :
- L'oxycoupage est plus économique en termes d'équipement et de consommation d'énergie, surtout pour les matériaux épais. Le coût du procédé est souvent plus bas, car il utilise moins d'énergie et des consommables relativement simples.
- Découpage plasma haute définition :
- Le coût d'équipement et d'exploitation est plus élevé pour le découpage plasma haute définition, principalement en raison du coût des machines et de la consommation d'énergie du plasma à haute température. Cependant, la précision et la qualité des découpes justifient cet investissement, surtout pour des travaux de haute précision ou pour des métaux non ferreux.
6. Maintenance et durée de vie :
- Oxycoupage :
- L'oxycoupage nécessite peu de maintenance si l’équipement est bien entretenu. Les consommables, tels que les buses et les filtres, ont une durée de vie raisonnable, bien que l'équipement puisse subir de l'usure à cause de la chaleur intense.
- Découpage plasma haute définition :
- Le plasma haute définition nécessite une maintenance plus fréquente en raison des éléments consommables comme les électrodes, les buses et les joints qui s'usent plus rapidement avec l’utilisation du plasma. Le matériel est généralement plus coûteux à entretenir.
Conclusion : Différences principales entre oxycoupage et découpage plasma haute définition
Critère | Oxycoupage | Découpage Plasma Haute Définition |
---|---|---|
Principe | Réaction chimique avec de l'oxygène | Plasma ionisé à haute température |
Matériaux | Principalement acier au carbone | Métaux ferreux et non ferreux (aluminium, inox, cuivre, etc.) |
Qualité de la coupe | Bords irréguliers, zone affectée thermiquement | Précision élevée, bords nets et propres |
Applications | Découpe de matériaux ferreux épais | Découpe de matériaux variés et de haute précision |
Vitesse | Rapide pour les matériaux très épais | Rapide pour les matériaux de moyenne épaisseur |
Coût | Moins cher en matériel et consommation d'énergie | Plus cher en matériel et consommables |
Entretien | Moins de maintenance | Maintenance plus fréquente et coûteuse |
Le choix entre oxycoupage et découpage plasma haute définition dépend principalement du type de matériau, de l'épaisseur du métal, de la qualité requise pour la coupe et du budget disponible.
Qu'est que le parachèvement de profil en acier ?
Quel accessoires de levage utiliser entre : le palonnier de levage, le cé de la levage, les élingues de levage, les manilles de levage, le palan de levage, la potence de levage, le monorail de levage ?
Le choix de l'accessoire de levage à utiliser dépend du type de charge, de l'environnement de travail, de l'usage spécifique et des exigences de sécurité. Voici un aperçu des différents accessoires de levage que vous avez mentionnés, leurs applications spécifiques et quand les utiliser :
1. Palonnier de levage
Description :
Un palonnier est un dispositif de levage conçu pour répartir uniformément la charge suspendue. Il se compose généralement de poutres horizontales équipées de plusieurs points de levage (œillets, crochets, etc.).
Applications :
- Utilisé pour soulever des charges lourdes et volumineuses qui nécessitent une répartition uniforme du poids.
- Permet de soulever plusieurs charges simultanément ou de soulever des charges de formes irrégulières (par exemple, des structures métalliques, des éléments de béton préfabriqué, etc.).
- Très utilisé dans les grandes industries, les chantier de construction ou pour manipuler des charges larges ou longues.
Quand l'utiliser ?
- Lorsque la charge est large, grande ou présente une forme irrégulière et qu'il faut la répartir de manière égale.
- Pour soulever plusieurs charges simultanément ou une charge nécessitant plusieurs points de levage.
2. Cé de levage
Description :
Le cé de levage est un accessoire spécifique qui est généralement utilisé pour faciliter le levage des charges avec des formes particulières, comme des cylindres ou des tuyaux. Il est conçu pour être intégré à un système de levage ou à un palonnier, permettant ainsi de stabiliser la charge pendant son levage.
Applications :
- Utilisé pour soulever des objets cylindriques, des tuyaux ou des charges longues.
- Permet de maintenir une charge en position stable pendant le levage, surtout si elle risque de se déséquilibrer.
Quand l'utiliser ?
- Lorsque la charge a une forme irrégulière, comme des tubes ou des barres, et nécessite un dispositif pour la maintenir stable.
- Lorsqu'il faut éviter le roulis ou l'oscillation d'une charge pendant son levage.
3. Élingues de levage
Description :
Les élingues de levage sont des dispositifs souples utilisés pour relier la charge à l'équipement de levage (palans, grues, etc.). Elles peuvent être fabriquées à partir de câbles métalliques, de chaînes, ou de fibres synthétiques (polyester, polyamide).
Applications :
- Utilisées pour lever des charges de toutes formes et tailles.
- Très polyvalentes, elles sont utilisées dans de nombreux secteurs comme la construction, l'industrie, le transport, etc.
- Les élingues peuvent être utilisées en mono-brin, double-brin ou en forme de boucle, selon la charge à soulever.
Quand l'utiliser ?
- Lorsque la charge est difficile à saisir ou de formes irrégulières.
- Pour soulever des charges moyennes à lourdes, souvent en combinaison avec un palan ou une grue.
- Lorsque l'espace est restreint et qu'il est difficile de positionner un palonnier ou une potence.
4. Manilles de levage
Description :
Les manilles de levage sont des accessoires de levage utilisés pour relier des équipements entre eux, comme un palonnier, une élingue, ou un point de levage. Elles sont généralement en acier forgé et équipées d'un goupillon ou d’un clip pour assurer un maintien sécurisé.
Applications :
- Utilisées pour raccorder des accessoires de levage entre eux ou avec la charge.
- Utilisées dans des environnements où les crochets ou autres systèmes de fixation doivent être solides et résistants.
- En combinaison avec des élingues, des chaînes ou des câbles.
Quand l'utiliser ?
- Lorsque vous avez besoin de raccorder des éléments entre eux (par exemple, pour fixer une élingue ou un palonnier à un crochet de grue ou à un point de levage).
- Lorsque la sécurité et la solidité des connexions sont essentielles.
- Pour des applications qui nécessitent des connexions rapides et solides.
5. Palan de levage
Description :
Le palan de levage est un équipement mécanique ou électrique permettant de soulever des charges verticalement. Il peut être monté sur des rails (palans suspendus), ou sur des supports fixes.
Applications :
- Utilisé pour soulever des charges lourdes ou de grande taille, souvent dans des environnements industriels ou de construction.
- Adapté pour des levages précis, avec des capacités de levage variées, allant de quelques kilos à plusieurs tonnes.
Quand l'utiliser ?
- Lorsque vous devez soulever des charges lourdes, difficiles à manipuler ou nécessitant des déplacements verticaux.
- Lorsque vous avez besoin de précision et de contrôle sur le levage.
- En combinaison avec des monorails ou des potences pour les levages dans un espace délimité.
6. Potence de levage
Description :
La potence de levage est une structure métallique qui permet de soulever des charges à l’intérieur d’un espace limité. Elle est généralement équipée d'un palonnier ou d'un palan pour effectuer les levages. Elle est fixée à un point d'ancrage fixe ou mobile et peut pivoter à 360°.
Applications :
- Utilisée pour des levages dans des espaces restreints, tels que des ateliers ou des entrepôts.
- Permet de déplacer des charges lourdes ou volumineuses sur une courte distance.
- Souvent utilisée dans des ateliers de maintenance, des usines ou des zones de production.
Quand l'utiliser ?
- Lorsque vous avez besoin de soulever des charges dans un espace limité, souvent dans des environnements industriels.
- Pour des levages horizontaux et verticaux à courte portée, où la portée du levage doit être limitée à une zone spécifique.
7. Monorail de levage
Description :
Le monorail de levage est un système de rails monté au plafond, permettant de déplacer une charge le long d'un axe linéaire. Il est souvent équipé d'un palan ou d'un chariot pour le déplacement de la charge.
Applications :
- Utilisé dans des installations industrielles pour transporter des charges le long d'un trajet défini.
- Permet de déplacer des charges lourdes sur une longue distance, souvent à l'intérieur d'un atelier ou d'un entrepôt.
- Particulièrement adapté aux applications en série ou pour le transport de charges lourdes d’un point à un autre.
Quand l'utiliser ?
- Lorsque vous devez déplacer des charges sur une longue distance dans un espace confiné ou une ligne de production.
- Pour des applications nécessitant un déplacement linéaire précis de charges lourdes ou volumineuses.
Conclusion
Le choix de l'accessoire de levage dépend des spécificités du levage à réaliser :
- Si la charge est lourde et volumineuse, un palonnier de levage ou une potence est souvent nécessaire.
- Pour des charges de forme irrégulière ou des charges longues, les élingues et le cé de levage seront privilégiés.
- Les manilles sont utilisées pour relier les accessoires entre eux, tandis que le palan et le monorail sont choisis pour le levage et le déplacement de charges lourdes sur une longue distance.
Chaque équipement a son domaine d’application spécifique, et il est essentiel de choisir l’accessoire adapté à la charge, à l’espace disponible et à la nature du travail.
-
Congès d'été 202426/07/2024Nous vous informons que nous serons fermés tout le mois d'août, du lundi 05 août au vendredi 30 août 2024. Nous serons de retour le lundi 02 septembre 2024 pour répondre à vos attentes et trouver conjointement les solutions adaptées à vos besoins. Nous vous souhaitons de bonnes vacances...
-
Trémie avec convoyeur kilométrique26/07/2024CHANTIER EN COURS !Notre dernière réalisation dans notre région, mise en service d'une trémie avec convoyeur kilométrique.Votre solution en manutention pour les produits en vrac et les charges isolées ! Fabrication française et sur mesure...
-
Nouvelle plaquette générale !23/01/2024Après de longs mois de travail et de collaboration au sein de notre équipe , nous sommes fiers de vous présenter notre dernière nouveauté : notre nouvelle plaquette générale Breschard !...
-
Nouvelle plaquette SKIP !29/01/2024Dans la continuité de notre travail, nous sommes fiers de vous présenter notre dernière nouveauté : notre nouvelle plaquette Skip Breschard...
-
Vidéo de présentation YouTube05/02/2024Apprenez à nous connaître en regardant la présentation générale de notre société. Bonne vidéo à tous ! N'oubliez pas de vous abonner et d'activer la cloche pour ne rater aucune vidéo...
-
Notre stock en A516 GR 70 (P355GH) et autres04/01/2024Nous vous informons que nous avons un stock d'acier spéciaux composé de : A516 GR 70 (P355GH) : - 1 tôle de 4800 x 2000 x 5- 1 tôle de 2900 x 2500 x 8- 1 tôle de 4100 x 2500 x 8- 3 tôles de 6000 x 2500 x 10- 1 tôle de 2100 x 1800 x 12- 8 tôles de 6000 x 2500 x 15- 1 tôle de 3000 x 3000 x 15- 1...
-
Distributeur de gel hydroalcoolique à pédale (sans contact)04/01/2024A la demande de nombreux clients et afin de lutter face au Coronavirus, nous avons fabriqué un distributeur à pédale de gel hydroalcoolique dont voici les principales caractéristiques : La voix du nord a écrit un article sur le distributeur de gel hydroalcoolique, dont voici le lien Orange actu a...
-
Nouveau site internet pour le Pôle serrurerie-métallerie-charpente04/01/2024Le pôle Serrurerie-Métallerie-Charpente de la société "Breschard" est heureux de vous présenter son nouveau site. Vous pouvez parcourir l'ensemble des pages pour connaître nos différentes prestations, ainsi que visualiser nos photos de "Réalisations" pour vous rendre compte de la qualité de nos services. Pour toute...
-
Ouverture des Ateliers, des bureaux et du service livraison26/07/2024Nous vous informons que les ateliers sont ouverts du lundi au vendredi de 8 h à 12 h et de 12 h 30 à 15 h 30. Les livraisons sont possibles de 8 h à 12 h, et de 12 h 30 à 15 h 00, au delà les camions ne seront pas acceptés. Les déchargements de camions soit : par chariot élévateur (maxi 1.5 t) par pont...
-
Rayonnement géographique - SAS Breschard04/01/2024Implantée au coeur de la région Nord Pas-de-Calais (59/62), la SAS Breschard rayonne sur toute la moitié Nord : de Dunkerque à Paris ... ainsi que sur le reste de la France Marseille, Lyon, Toulouse, Nice, Nantes, Strasbourg, Montpellier, Bordeaux, Lille, Rennes, Reims, Le Havre, Saint-Étienne, Toulon, Grenoble, Dijon, Angers, Nîmes, Villeurbanne,...
-
Votre interlocuteur en matériels de manutention26/07/2024Depuis février 2018, Mr Anthony Ribeiro a remplacé Mr Bastien Bigotte au poste de chargé d'affaires "Matériels de manutention continue" Depuis 1923, SAS Breschard a axé son activité sur la réalisation de systèmes de manutention continue pour produits en vrac. Notre...
-
Votre interlocuteur en skips et matériels de levage26/07/2024Depuis Septembre 2018, Mr Antoine CREPIN a remplacé Mr Olivier CABARET au poste de chargé d'affaires "Skips et matériels de levage" N’hésitez pas à le consulter si vous avez besoin de skips, retourneurs et basculeurs ou matériel de levage (palonnier, cé de levage, double cé de levage, panier de levage, accessoires de...
-
Service oxycoupage et perçage.26/07/2024Le service oxycoupage est capable de faire des perçages dans des pièces rectangulaires jusqu'à 800 mm de large pour les trous inférieurs à l'épaisseur, par exemple faire des trous de 25 dans des épaisseurs de 50 mm. cela est possible en jumelant notre ligne de perçage/sciage et notre oxycoupage. Possibilité de...
-
Nouveaux Palonniers et Accessoires de Levage Sur-Mesure – Fabrication Française Certifiée CE27/05/2025Nouveaux Palonniers et Accessoires de Levage Sur-Mesure – Fabrication Française Certifiée CE Texte : Chez Breschard, nous innovons en permanence pour répondre aux besoins spécifiques de nos clients en matière de levage et manutention. Nous sommes fiers de vous présenter nos dernières réalisations : ✅ Palonniers sur-mesure...
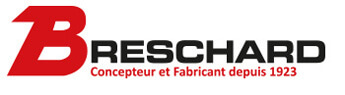
Nous sommes ouvert du lundi au Vendredi de 8 h à 17 h !